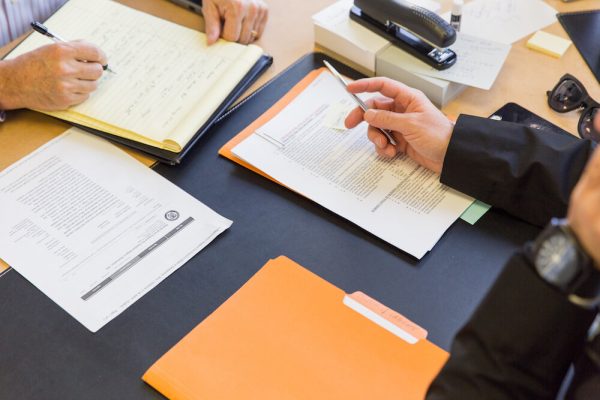
Predictive Key Performance Indicators (KPIs) are forward-looking; they can drive and influence results in a construction project. Here are five predictive KPIs to consider:
Bid Development
Contractors often describe the funnel of business development as getting a certain number of bids into the top of the funnel in order to get the desired amount of work to come out the bottom.
A forward-looking KPI could be developed to track some of the following inputs:
-
Pending bids currently in preparation
-
Business development meetings scheduled and completed
-
Active prospects and probability of winning work
-
Meetings a subcontractor has with existing and new GCs to gain new work
Management can set reasonable weekly, monthly, quarterly or annual expectations of these inputs and rationally predict outcomes well in advance. It may help management to know if indicators are slipping or surging when making staffing, purchasing and bidding decisions.
For example, if revenue-driving activities have been increasing over the past two-quarters, then management may be less willing to buy low margin work and more likely to make an opportunistic hire. On the other hand, if business development activities are unusually low, then that may be the indicator management needs to readdress the current overhead structure and consider tightening up for a predicted decrease in revenues.
Buyout Process
When a project is won, the construction manager (CM) immediately begins the buyout process. Management tracks the buyout percentage constantly, with an eye for potential problems. Slow buyout is frequently blamed for job fade later in the project, but may be predictable and preventable if monitored.
While this may appear to be a KPI only for CMs, subcontractors can measure the amount of time between when a CM wins work and contacts the subcontractor or buys out the related work. The greater the time span, the louder the signal that there may be schedule issues manifesting that could affect the subcontractor.
Quality Control
Companies can put forward-looking indicators into place to increase the level of quality in completed jobs. Highly technical projects often have increased engineer involvement, a set number of owner inspections, building infrastructure monitoring updates, formalized architect sign-offs/inspections, and other levels of monitoring.
Jobs with quality surprises often miss inspections and appropriate documentation. CMs can set the expectation for tracking key indicators early in the project and insist on periodic reporting.
A common approach to monitoring quality control is to conduct an independent review of all jobs that present a significant risk to the company. An internal senior committee often performs these at agreed-upon milestones to look at what levels of review are occurring, determine where additional quality control reviews may be conducted, and ensure that any additional quality control measures are carried out.

Subcontractor Inventory
Sometimes companies assume that the materials they use are consistent from job to job and there is little risk of over-purchasing. However, the economic downturn revealed buildups in both unique and common inventory far in excess of future job needs. When unneeded inventory builds up, precious cash is taken out of circulation. Also, bonding credit is rarely extended to inventory.
A simple series of leading indicators can verify that periodic inventories are occurring. This helps compare monthly purchasing activity to inventory on hand, identifying instances of purchasing inventoried stock. A KPI may be a simple exception report that compares monthly purchases of materials with unchanged primary location inventory of the same items.
With this information, management can investigate why inventoried items are being purchased and improve practices. Using inventoried materials instead of double purchasing can increase margins by 100% on items that may not be used again, which can greatly improve cash flow.
Safety
While a low experience modification rate or a high number of days without lost work demonstrates a safe past, a predictive KPI might be the number of safety activities currently implemented that includes the number of safety meetings, communications, notifications or awards that recognize someone doing something safe. Other examples may include team-wide “near miss” meetings or self-audits of OSHA preparedness.
When you hear of a company with an accident or fatality, how often do you hear them say that they had an exemplary record? A great safety record is obviously a good thing but is not necessarily a predictor of future success.